Motoral ships dangerous goods safely and efficiently with nShift
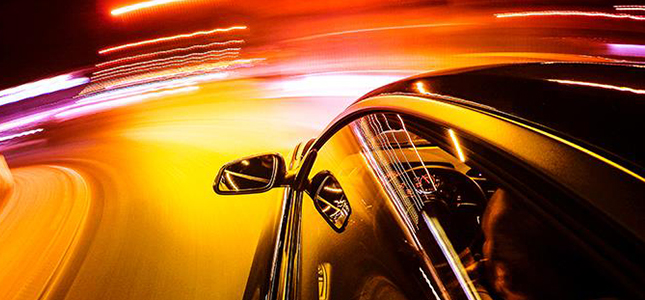
No video selected
Select a video type in the sidebar.
The Challenge
When companies and online retailers ship dangerous goods, they have to document all the details of the shipment to the carrier, including material name, danger category, UN number and so on. All this documentation is essential, as it tells the carrier how to handle the dangerous goods safely – but it also takes up a lot of time.
For Finnish auto parts wholesaler, Motoral, the process was proving especially burdensome. Jussi Vuorela, Logistics Planner at Motoral explains: “60 of our 300 daily shipments are categorized as dangerous goods shipments. So, every day, we have a large amount of dangerous goods documentation that we need to make sure is updated correctly and sent to the carriers.
Motoral were looking for a delivery management platform that would enable them to automate the entire dangerous goods shipping process and so save them from drowning in all the necessary documentation work.
It is crucial for us that our delivery management software supports dangerous goods. [nShift] is the only delivery management provider on the market that does this.
Jussi Vuorela, Logistics Planner at Motoral
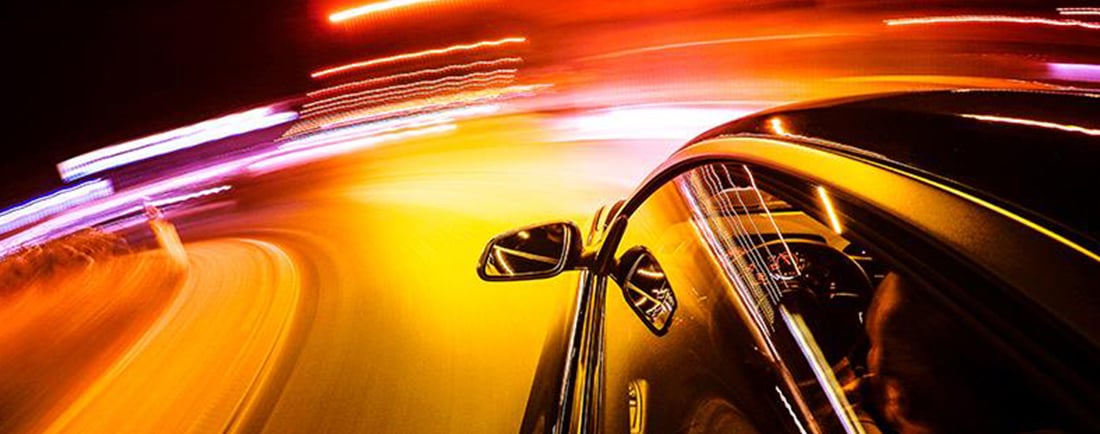
The Solution
Through nShift, Motoral has now automated the printing of all its dangerous goods documentation. All Motoral needs to do is set up its dangerous goods articles in the online catalog and nShift takes care of the rest – including transferring the required EDI to the carriers. This way, Motoral saves manual working hours, and is secured against potential fines and avoidable accidents due to poor documentation.
The Results
Implementing nShift has made life much better for Motoral workers. “Our warehouse employees spend much less time on shipping parcels because they don’t need to print labels and shipping documents manually,” says Jussi Vuroela. “They also don’t have to book shipments in different carrier systems. [nShift] does this automatically in one overall system.”
And It’s not just employees who benefit. It’s Motoral’s customers too. Jussi Vuorela: “We reduce our customers’ shipping costs when they buy multiple items, because we automatically consolidate their orders in [nShift]. It also allows us to track and trace.”
60 of our 300 daily shipments are categorized as dangerous goods shipments. So, every day, we have a large amount of dangerous goods documentation that we need to make sure is updated correctly and sent to the carriers. In order for us not to drown in documentation work we have chosen to automate the entire dangerous goods shipping process by using [nShift].
Jussi Vuorela, Logistics Planner at Motoral
Are you ready to get started?
