Wittusen & Jensen saves a salary a year with nShift QR codes
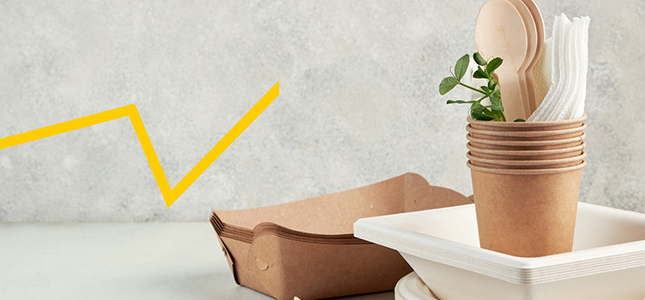
No video selected
Select a video type in the sidebar.
The Challenge
Camillia Haltbakk, Operations Manager at Norwegian office supplies and consumer goods wholesaler, Wittusen & Jensen, was looking for a way to save the company money by handling parcels more efficiently. She was also fascinated by the possibilities offered by QR codes.
So, in 2015, she and members of Wittusen & Jensen’s IT team joined forces with nShift to see if QR codes could be used to help the company work more efficiently.
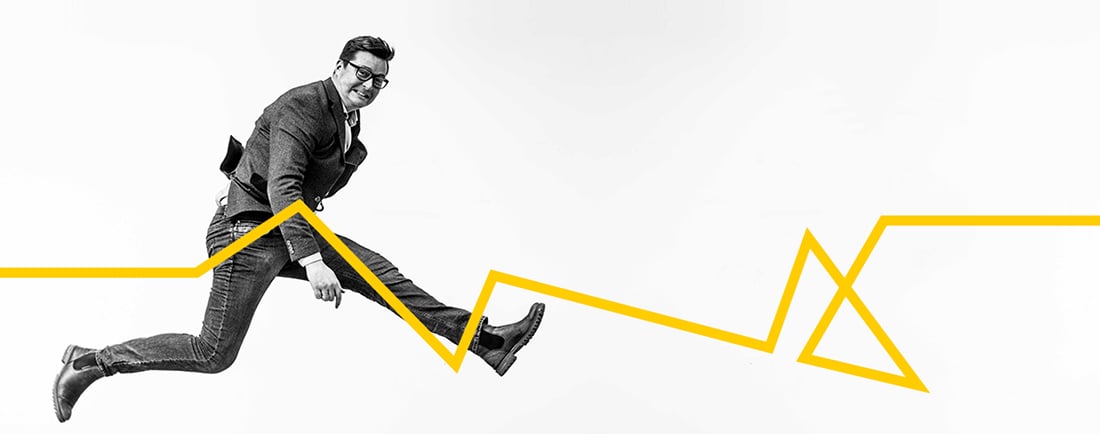
The Solution
Freight labels with QR codes are printed and applied automatically at Wittusen & Jensen’s central warehouse just outside Oslo via a hydraulic printer on a conveyor belt and on forklifts during the picking process.
Camilla Haltbakk explains: “We were already using [nShift] to print freight labels and transfer shipment data to carriers and it was no problem to add the QR codes to the existing labels. Now, when customers receive our packages, they are able to scan the QR code and see a digital delivery note with information about the entire consignment’s contents. That way, it is easier for them to keep track of consignments divided into several deliveries.”
The new system saves the company time and money in the warehouse as well. “We print labels on board the forklifts that drive around the warehouse picking larger items. That way we save time, as the items get a freight label as soon as they are picked. [nShift] ensures that the correct freight label is printed on the forklift printer by retrieving the shipment data from our ordering system.”
The Results
Given that Wittusen & Jensen sends more than 400,000 parcels every year, any time saved during the delivery process can make a significant difference to the bottom line – and this has certainly been true of the introduction of QR codes.
“We are able to save the equivalent of an entire annual salary, as we don’t have to get an employee to put delivery notes in each and every parcel,” says Camilla Haltbakk. “We also save money on paper, toner and maintenance of printers. In addition, the number of inquiries from customers in connection with partial deliveries is reduced as they are able to see the entire delivery, what has been ordered and delivered via the digital delivery note.”
We send more than 400,000 parcels every year. We are able to save the equivalent of an entire annual salary, as we don’t have to get an employee to put delivery notes in each and every parcel. We also save money on paper, toner and maintenance on printers.
Camilla Haltbakk, Operations Manager at Wittusen & Jensen
Are you ready to get started?
