Customers love what we do
Cor Rijken Verpakkingen bags a first-class solution with nShift
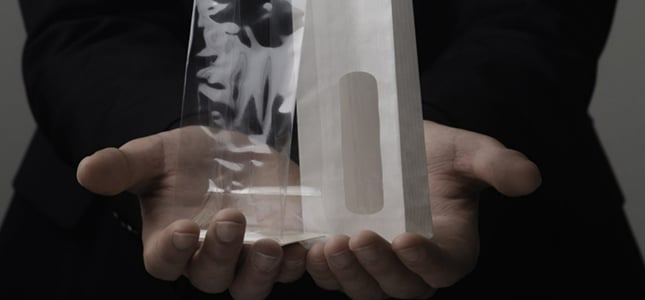
No video selected
Select a video type in the sidebar.
The Challenge
Launched by Cor Rijken himself in an attic room in 1990, Cor Rijken Verpakkingen now produces more than 70 million packages a year in its own production facilities, and a further 100 million packages elsewhere. Willem Sangers, a manager responsible for sales and logistics at Cor Rijken Verpakkingen, says: "By now we export to about 40 countries worldwide – our packaging is even used in Australian supermarkets. Very cool! We mainly produce and supply our standard range, both printed and unprinted. But if there is a specific occasion for which a bag needs to be made, we are happy to provide our customers with appropriate custom advice."
Given the size and complexity of Cor Rijken Verpakkingen’s logistics process, efficiency is paramount. So when the company was introduced to nShift, via their ERP provider, AFAS, they saw a fantastic opportunity to automate their system, saving time and reducing errors.
The system is much less error-prone because everything is automated. A first-class solution for us!
Willem Sangers, Business Manager at Cor Rijken Verpakkingen
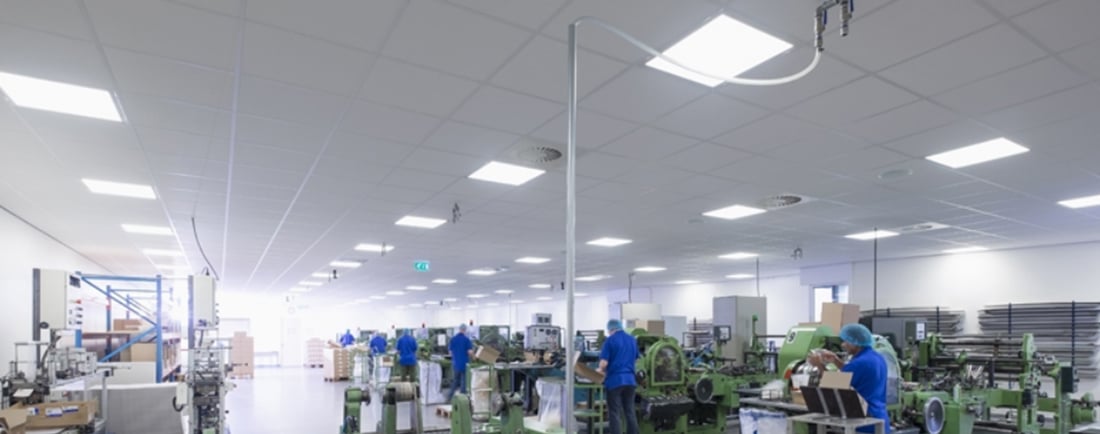
The Solution
By integrating nShift with AFAS, Cor Rijken Verpakkingen can now link to more than 400 carriers worldwide directly from their own ERP environment. This saves considerable time. It also increases flexibility, which is critical for a company like Cor Rijken Verpakkingen that specializes in custom-made products. Willem: "It is still possible to maintain our personal approach: everything can be adjusted to our wishes and those of our customers. This is how we can distinguish ourselves in the market."
The Results
Willem has been very satisfied with the performance of nShift so far. As well as saving time and reducing errors, the platform has made it much quicker and easier to onboard new carriers. He explains: “We just negotiate with the carrier. Other than that, we don’t have to take any steps. [nShift] makes all the adjustments and the shipping labels come out right away because everything is automated. It really runs like a well-oiled machine!"
It really runs like a well-oiled machine!
Willem Sangers, Business Manager at Cor Rijken Verpakkingen
